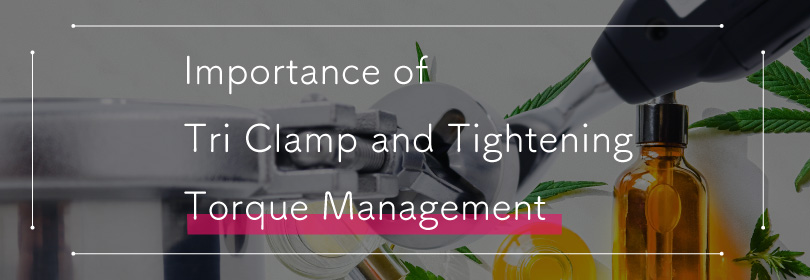
In a CBD production plant, it is very important to control the storage conditions of the product. In some cases, highly cleanable tri-clamp rings are used for piping in production equipment.
Tri-clamp rings do not require tools and can be installed manually, but the disadvantage is that the tightness of the clamp ring is determined by the operator’s senses and experience.
When we talk about “tightening” something, we tend to think to tighten something so firmly that the object is fixed and does not move.
However, “tighten it firmly” is not necessarily equal to “tighten it strongly”. It is important to tighten with the appropriate torque. Excessive tightening risks deforming or damaging the parts.
Another equally important issue is to be careful about gasket overflow due to over-tightening. The gasket between the piping or between the lid and the container may protrude inside or outside the container or piping, resulting in poor sealing or foreign matter contamination.
In this column, we will focus on the inside protrusion of the ferrule gasket. We will also conduct an experiment to see how much the gasket protrudes depending on the tightening torque when ferrule is tightened with a tri-clamp.