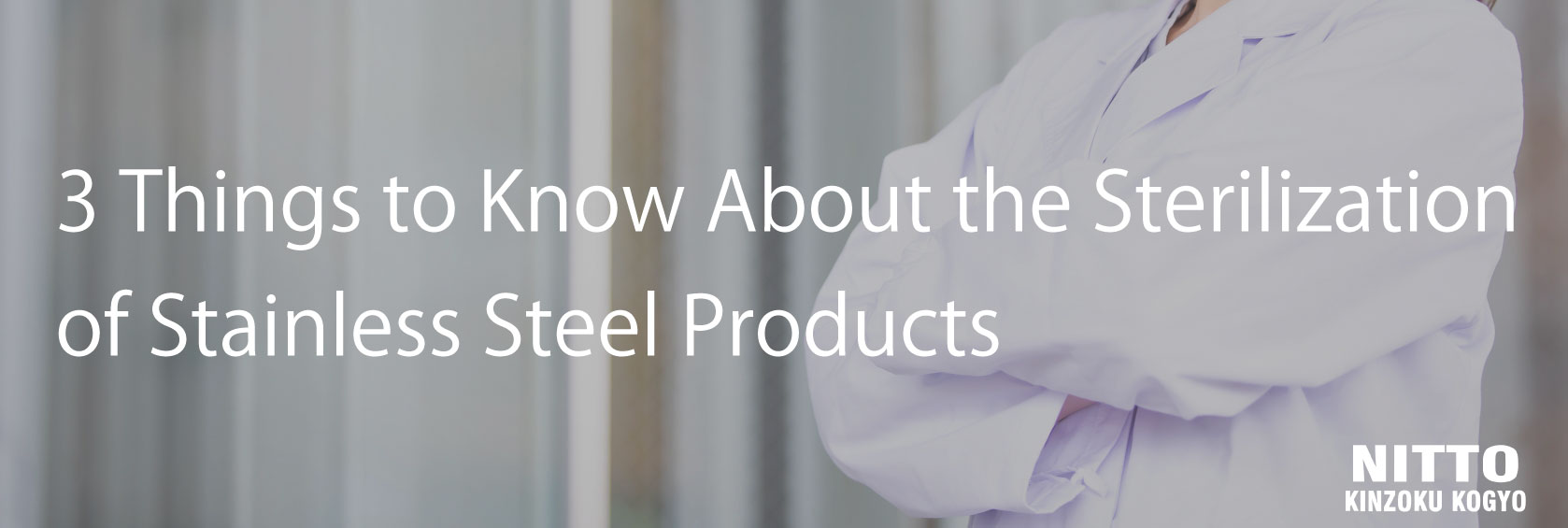
Although stainless steel is a kind of material that can be sterilized, but only a part of stainless steel products can be sterilized, while others cannot.
Despite there are various types of sterilization, we will introduce the case of autoclaving (High-pressure steam sterilization / 121 ° C for 20 minutes) the stainless steel containers manufactured by Nitto Kinzoku Kogyo.
Please feel free to contact us regarding the sterilization of our products.
Contents
- Is it possible to sterilize stainless steel products?
- What should we be careful when sterilizing the stainless steel products?
- Will stainless steel products get rusty after the sterilization?
- Especially recommended stainless steel products for sterilization purpose
- Actual instances related to sterilization